伺服壓力機是由伺服電機驅(qū)動高精度滾珠絲桿(伺服電動缸),通過控制電機轉(zhuǎn)動角度實現(xiàn)對壓頭的精準位置控制。壓頭前端安裝高靈敏壓力傳感器,采集實時壓力,實現(xiàn)壓力閉環(huán)控制。通過高速采集壓裝過程中的位置壓力數(shù)據(jù),實現(xiàn)精密壓裝的在線質(zhì)量判斷和數(shù)據(jù)信息化管理。
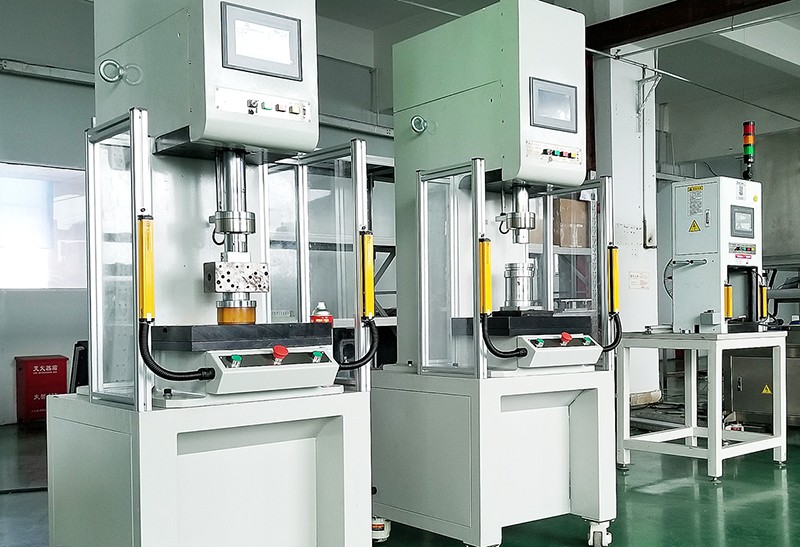
伺服電機驅(qū)動:全過程閉環(huán)控制,實時監(jiān)控壓力、距離和速度。可精確控制壓頭的位置和速度。實現(xiàn)高精度、可控制的壓接,有效避免過壓和欠壓。
壓力傳感器:裝配大小兩組壓力傳感器,最低可偵測力為1磅。
多樣的壓接技術(shù):PFT(壓接壓力)、PHT(壓接高度)、CAT(壓接曲線角度)、FST(壓接采樣) 等工作控制模式,實現(xiàn)產(chǎn)品精密壓接。采用觸摸式顯示屏,給人機交互帶來極大的便利性。極簡的編程以及智能設(shè)置的數(shù)據(jù)庫,通過參數(shù)設(shè)定實現(xiàn)壓接精度控制,產(chǎn)品設(shè)置換型不需要任何的硬件調(diào)整。
運動控制:全過程閉環(huán)控制,實時監(jiān)控壓力、距離和速度,可精確控制壓頭的位置和速度。
生產(chǎn)追溯系統(tǒng):數(shù)據(jù)保證每次壓接的質(zhì)量和可追溯性,可數(shù)據(jù)收集/顯示/打印。壓力曲線自動保存/分析軟件包,對壓接制程提供全面的數(shù)據(jù)管理。
伺服壓力機,凱鈺伺服電動缸是與傳統(tǒng)機械壓力機完全不同概念的壓力機,它是高新技術(shù)與傳統(tǒng)的機械技術(shù)的結(jié)合,實現(xiàn)了沖壓設(shè)備的數(shù)字化控制。伺服壓力機采用單個或多個伺服電機,通過雙驅(qū)動機構(gòu)和對稱增力機構(gòu),直接驅(qū)動滑塊的主傳動結(jié)構(gòu)形式,控制系統(tǒng)采用計算機控制,利用數(shù)字化及反饋控制技術(shù),對壓力機滑塊未知,速度,運行軌跡實現(xiàn)控制,使機械壓力機具有柔性化,智能化的特點,工作性能和工藝適應性大大提高,是成型裝備的一個重大突破。
一、伺服壓力機技術(shù)
隨著大功率伺服電機的研發(fā)成功和變頻技術(shù)得到迅速的推廣應用,出現(xiàn)了滑塊運動曲線可調(diào)的伺服壓力機,使得壓力機的工作性能和工藝實用性大大提高,壓力朝著柔性化,智能化的方向發(fā)展。
經(jīng)過多年的發(fā)展,伺服技術(shù)已經(jīng)在壓力機領(lǐng)域得到了廣泛應用。在制品成形壓力機,汽配零件壓裝壓力機領(lǐng)域,經(jīng)過眾多從業(yè)技術(shù)人員的努力,伺服技術(shù)也已經(jīng)開花結(jié)果,在金屬沖壓行業(yè),汽配電機軸承壓裝行業(yè)和耐材制品行業(yè)得到認可,開始為越來越多的生產(chǎn)企業(yè)所接受。
二、伺服壓力機工藝
壓力裝配作業(yè)是機械工程中常用的工藝方法。特別是在汽車和汽車零部件行業(yè)中,軸承、襯套等零件的裝配都是采用壓力裝配實現(xiàn)的。
伺服壓力機作為一種新的技術(shù),有著傳統(tǒng)液壓壓力機不具備的優(yōu)勢,在汽車制造工藝環(huán)節(jié)如缸蓋氣門座圈和導管壓裝、缸體水道堵蓋壓裝、變速器軸承壓裝、輪轂軸承壓裝等工藝中,正隨著設(shè)備更新等方式逐步替代傳統(tǒng)的液壓壓力機,有效提升了汽車制造工藝水平。
就拿軸承壓裝來說,軸承是運動部件,壓裝的效果直接影響車輛或者是產(chǎn)品設(shè)備的性能和壽命。軸承對受件的鏜孔加工的公差要求越高,在軸承的壓裝過程中有效監(jiān)控壓裝力和位移就越重要。傳統(tǒng)的壓裝有液壓或者是氣壓為動力的壓裝設(shè)備,該壓裝設(shè)備在壓裝過程中因為不能有效控制壓裝的壓力和位移,因此會因為壓裝力瞬間過載而導致軸承卡死無法轉(zhuǎn)動或者是轉(zhuǎn)動不靈活。而伺服壓力機驅(qū)動動力源采用具有智能、柔性、靈敏的伺服電機控制,結(jié)合壓力傳感器,因此壓力,位移,速度精確可調(diào),可以很好的解決因為速度及壓力的原因造成壓裝過載,同時配合壓裝力和位移的在線監(jiān)測,能有效判斷壓裝效果,壓裝參數(shù)可以保存,實現(xiàn)主機廠對壓裝部件的可追溯性。類似精密要求的工藝在壓裝時都適合用伺服壓力機凱鈺伺服電動缸來完成。
三、使用伺服壓力機后優(yōu)勢的體現(xiàn)
傳統(tǒng)的曲柄壓力機滑塊運動曲線固定,工藝適應性差,而且噪音大、能耗高。與傳統(tǒng)曲柄壓力機相比,現(xiàn)代伺服壓力機采用交流伺服電機代替普通交流電機,去除了傳統(tǒng)曲柄壓力機上的飛輪和離合器。通過計算機及智能控制技術(shù),現(xiàn)代伺服壓力機可以任意設(shè)定滑塊的運動曲線,工藝適應性強、噪音小、能耗低,能大幅提升生產(chǎn)效率。伺服壓力機代表了壓力機的發(fā)展方向,研究基于伺服電機直接驅(qū)動的伺服壓力機凱鈺伺服電動缸,具有重要的經(jīng)濟與社會意義。
1.提高生產(chǎn)率行程長度可設(shè)定為生產(chǎn)必要的zui小值,可維持與加工內(nèi)容相適合的成型速度;
2.制品精度高,通過閉環(huán)反饋控制,始終保證下死點的精度,抑制產(chǎn)品出毛邊,防止不良品的產(chǎn)生;
3.噪音低,模具壽命通過低噪聲模式(即降低滑塊與板料的接觸速度),與通用機械壓力機相比,大幅減少噪音,而且模具的振動小,壽命長;
4.滑塊運動的可控制性使用者可利用此特點編制出適合于加工工藝的滑塊運動方式,有效提高產(chǎn)品的精度和穩(wěn)定性,提高模具壽命及生產(chǎn)率,而且可實現(xiàn)靜音沖裁,甚至可擴大加工范圍(如鎂合金的沖壓加工等),適用于沖裁,拉深,壓印和彎曲等工藝,以及不同材料的特性曲線,如可將滑塊運行停止保壓,其目的是提高制件的成型質(zhì)量。
5.節(jié)能環(huán)保取消了傳統(tǒng)機械壓力機的飛輪,離合器等耗能元件,減少了驅(qū)動間,簡化了機械傳動結(jié)構(gòu),自動化潤滑,行程可控,由于電力消耗少,因此運行成本也大幅降低。
與傳統(tǒng)壓力機相比,伺服壓力機凱鈺伺服電動缸不僅具有液壓機的工作平穩(wěn),行程,壓力可調(diào)的優(yōu)點,還具有傳統(tǒng)機械壓力機結(jié)構(gòu)簡單,生產(chǎn)率高的優(yōu)點,其獨自的特點和優(yōu)點:調(diào)高設(shè)備自動化,智能化水平,實現(xiàn)數(shù)字化控制,實現(xiàn)了普通機械壓力機所不能達到的壓力成型工藝,改善壓力機的工作特性,節(jié)能環(huán)保,提高模具壽命,簡化機械傳動機構(gòu),安全性高,可靠性高,維修性好,設(shè)備通用性高,以及具有壓力機運行信息管理功能和生產(chǎn)信息管理功能等。
四、伺服壓力機壓裝模式的設(shè)定
1;恒定壓裝速度,設(shè)定精確位置停止。
2;恒定壓裝速度,設(shè)定精確壓力停止。
3;恒定壓裝速度,設(shè)定精確位移停止 。
4;恒定壓裝速度,I/O觸發(fā)停止。
5;壓力/位移,兩段式模式。
6;壓力/壓力,兩段式模式。
7;壓力/位置,兩段式模式。
五、伺服壓力機壓裝流程
單沖程六段速:
快進:快速接近工件
探測:從空載到載車檢測
壓裝:工件壓入
緩沖:壓裝終止前減速
保壓:壓裝終止位停留
返回:快速返回工作原點
整個壓裝過程分為快進、探測、壓裝、緩沖、保壓、返回六個階段。
【自動狀態(tài)】開機時設(shè)備自動尋找機械原點,設(shè)置好參數(shù)后,雙手按下啟動按鈕壓頭將在此位置以快進速度(即壓頭在接觸壓裝試樣的行進過程)下降到探測位置,然后以探測速度下降(即為在接觸試樣的短暫過程中,設(shè)定的壓裝區(qū)域位置對應的壓力是否在允許范圍內(nèi)),開始探測過程。探測過程直到所設(shè)定的探測限制位置為止,如到了探測限制位置還未探測到工件,壓頭將停止動作(此功能避免壓裝工件失敗),此時可按回按鈕返回機械原點;當在探測過程接觸壓力達到設(shè)定值時,壓頭自動切換到壓裝速度開始壓裝工件,壓裝到一定位置時以緩沖速度繼續(xù)對工件進行壓裝,壓裝到指定位置后將按用戶所設(shè)定的保壓時間保壓,保壓時間到壓頭以設(shè)定速度返回至所設(shè)置的工作原點凱鈺伺服電動缸。
在六個階段動作運行時,控制系統(tǒng)自動完成對數(shù)據(jù)的采集、分析、診斷、存檔工作,實時保證各階段壓裝的可靠性。
【手動狀態(tài)】可寸動伺服【快/慢】【上/下】
六、伺服壓力機未來趨向
伺服壓力機技術(shù)的應用為現(xiàn)代機械的精確精密智能控制打開了一扇大門,伺服壓力機在壓裝工藝的應用已經(jīng)展示出其明顯優(yōu)勢,在產(chǎn)品成形、自動化實現(xiàn)、模具壽命、能源利用、故障率等多個方面也都擁有明顯的優(yōu)勢,隨著國內(nèi)3C電子、新能源汽車等產(chǎn)業(yè)的高速增長,市場對制造設(shè)備的智能化要求高漲,中國運動控制行業(yè)在技術(shù)革新和市場運營方面的發(fā)展速度加快,伺服壓力機顯然已成為精密智能化壓裝產(chǎn)線的主流設(shè)備,正在大幅度的占據(jù)各行各業(yè),屬于伺服壓力機的時代,真正到來。